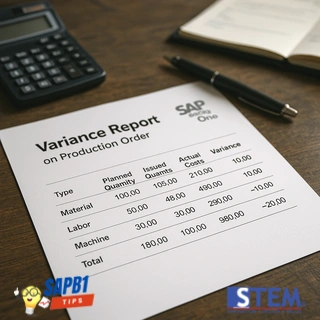
In manufacturing management, production efficiency is one of the critical aspects that must be considered. One tool to evaluate such efficiency is the Variance Report on Production Order in SAP Business One. This report provides information on the differences between production plans and actual outcomes, which is highly beneficial for analysis and decision-making.
What Is a Variance Report?
A Variance Report is a report that highlights the difference between planned data and actual data during the production process. In the context of a Production Order in SAP B1, this report includes information on:
- Item used.
- Resource utilized (e.g., labor or machinery).
- Production costs.
- Production output quantities.
This report enables companies to identify areas that need improvement, such as excessive item usage, inefficient resource utilization, or cost discrepancies.
Key Components of the Variance Report
- Item Variance
- Compares the planned quantity of items with the actual quantity used.
- Identifies whether items were used more or less than planned.
- Resource Variance
- Highlights the difference between planned and actual resource usage during production.
- Measures the efficiency of resource utilization in completing the Production Order.
- Cost Variance
- Illustrates the gap between planned costs and actual costs incurred.
- Provides insights into whether the production process was more cost-effective or expensive than anticipated.
- Production Quantity Variance
- Compares the planned production output quantity with the actual quantity produced.
- Identifies whether there is overproduction or underproduction.
Common Sources of Variance
- Inaccurate Planning
Errors in estimating items, resources, or costs are often the main causes of variance. - Operational Issues
Problems such as machine breakdowns, supply chain disruptions, or procedural errors can impact actual outcomes. - Changes to Production Orders
Modifications to the production plan midway through the process can result in discrepancies between the plan and realization. This difference may occur because the quantity of components used in production exceeds the budgeted amount, resulting in a negative variance, or the quantity of components used is less than planned, leading to a positive variance. - Item Quality
Low-quality or defective items can increase material usage and costs.
How to Access the Variance Report in SAP Business One
- Navigate to the Production > Production Order.
- Find the Production Order document for which you want to display the Variance Report.
- Right-click on the relevant Production Order and select Variance Report from the context menu.
- The Variance Report will display data such as comparisons of planned and actual quantities, costs, and resource efficiency.
- Variance Report in SAP Business One includes the following details:
- Type: Indicates the type of component (e.g., Resource Component, Item Component, Product, etc.).
- No.: Reference number for the component or resource.
- Description: A brief description of the component or resource.
- Qty: Quantity used.
- Cost: Average cost per unit.
- Total: Total cost for the component.
- Variance: Difference between planned and actual costs or quantities.
For example, a manufacturing company produces “Tas Kulit” with planned resources “Cutting” machine (RTA50001) and materials “Kulit Sintetis” (TAS0001). After production is completed, discrepancies are found between the planned and actual usage of specific resources and items. The Variance Report reveals:
- Resource “Cutting”: A cost variance of AUD -1,000 indicates that the actual cost for the cutting process was higher than planned. This may be due to longer labor time, machine breakdowns increasing process time, or unexpected additional costs.
- Item “Kulit Sintetis”: A cost variance of AUD -900,000 suggests that more material was used than planned. This could be caused by material waste, defective products requiring additional materials, or errors in the initial quantity estimate.
In this situation, the production manager needs to investigate the root causes of the variances to take corrective actions, such as improving planning, increasing resource utilization efficiency, or ensuring better item quality to minimize waste.
Steps to Minimize Variance
- Improve Planning
Use historical data to enhance the accuracy of production planning. - Optimize Production Monitoring
Ensure the production process is well-supervised to identify issues in real time. - Train Employees
Improve employee skills to minimize operational errors. - Regularly Audit Items, Resources, and Costs
Conduct periodic reviews to ensure item, resource, and cost usage aligns with plans.
Benefits of the Variance Report
- Enhancing Efficiency
Enables companies to identify and reduce resource waste. - Optimizing Costs
Helps control expenses that deviate from the plan. - Supporting Production Planning
Provides more accurate data for future planning. - Improving Decision Quality
Delivers relevant data for in-depth analysis and strategic decision-making.
The Variance Report on Production Order in SAP Business One is a crucial tool for monitoring production process performance and efficiency. By utilizing this report, companies can identify variance causes, take corrective actions, and enhance overall operational efficiency. Consistent usage and in-depth analysis of this report can provide competitive advantages for companies in the long term.
Also read:
- How to Record Cost of Resources in the Production Process
- How to Return Components Have Been Used in a Production Order
- By-Product in Production Documents
- Update the Production Order After Closed or Canceled
- Production Issue Method: Backflush vs Manual
- Production Standard (Std) Cost Rollup
- Maintain Status Multiple Production Order